MBM Turnkey Crossing Systems
MBM Crossings Installed
Feet of Crossing Installed
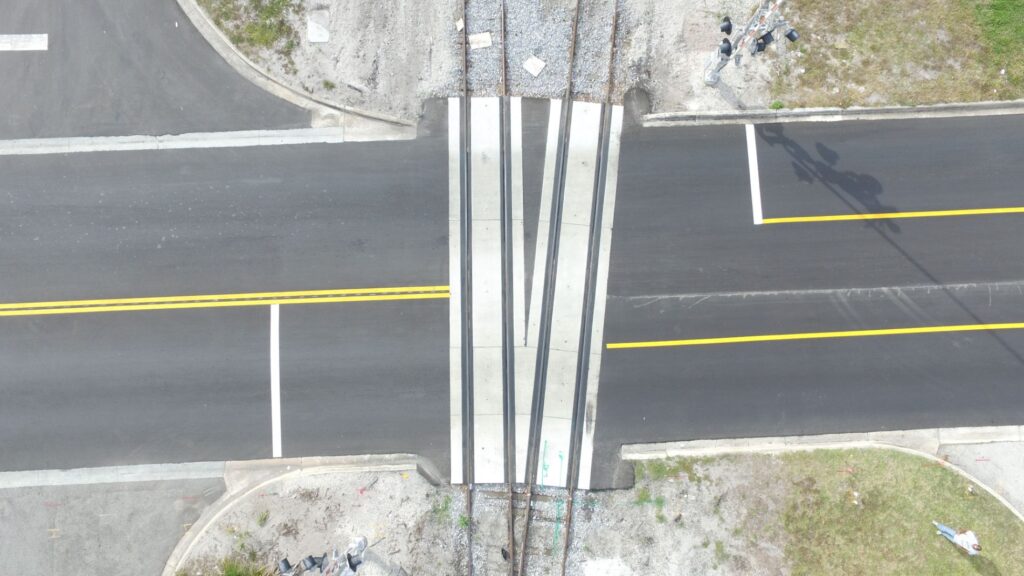
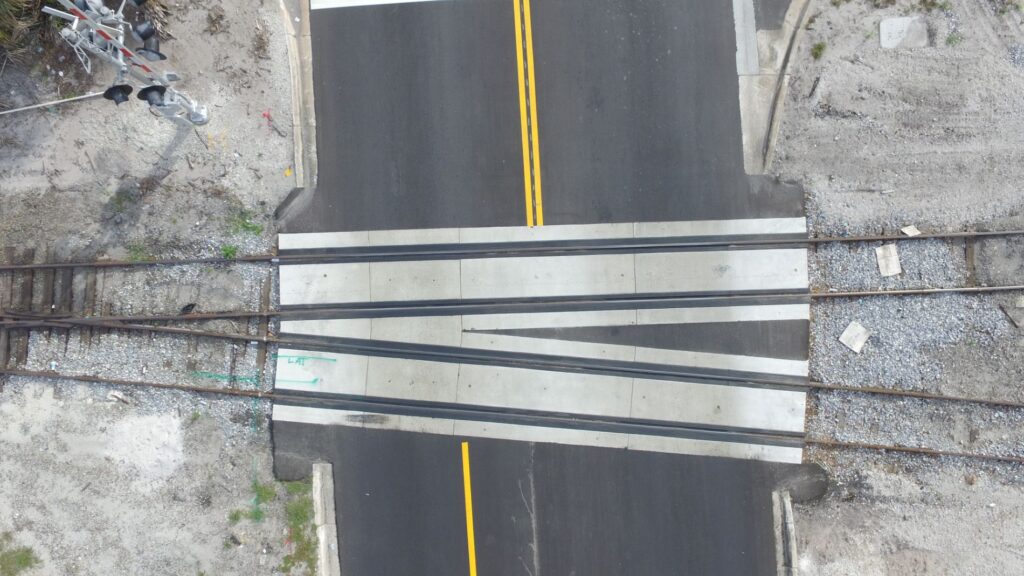
Seeing the failures of wood-based or full-depth rubber railroad crossings over time, Charles Merritt, former owner of R.W. Summers, “saw a need for a different crossing made with solid integrity.”
His answer was the development of the company’s own MBM Crossing Systems. Manufactured in-house, these systems have met the test of durability, as some MBM Crossings in Florida are 20 plus years old and holding up well.
Making the crossings durable is the more than 1,300 feet of rebar and nine yards of concrete that goes into them, and distribution of weight – their No. 1 advantage over competitors. Instead of distributing weight over a few crossties, MBM crossings do so over the entire system. And considering the way in which systems are joined to the rail and the grouting underneath, basically the entire crossing bears the weight. “There is no settlement,” says Merritt, from uneven distribution.
Years of Installation
Crossing Lifespan (Years)
The process of building a crossing begins in the yard of R.W. Summers. First, the rebar is set into a preset mold. Next the concrete is poured. Moving on down the rail, the panel is cleaned and smoothed into absorption pads that house a Pandrol clipping system. The studs are part of a stainless-steel anchoring system.
Installing the crossing system begins with removal of the existing track and the building of the grade upon which each MBM panel is placed. The company’s special screening system ensures a perfect grade.
The bed is leveled off and base material installed. The panel is then lowered into the framed area. Each panel has three grout holes, with channels underneath the concrete. Once the panel is in place, grout is injected underneath the panel to get rid of any voids. The continuous welded rails are set in place and clipped to pre-gauged plates. Asphalt is then installed, and grading work completed. The end result is a continuous welded rail embedded in a continuous solid system.
Installation for up to 60-foot crossings can be done within daylight hours. Crossings of 100 to 120 feet can be completed within 36 hours. Three hours after installation, vehicles can drive over the crossing.
The MBM Crossing is a total in-house effort of R.W. Summers, who makes AND installs them. “You buy it, you bought it installed,” says Merritt.